Stairs are a component of 99% of all projects.
Advance Steel has its own way of dealing with stairs, which makes the creation of stairs an easy process. In this tutorial, we will describe all the available aspects of creating and modifying Straight Stairs .
Note: If you want to create Spiral Stairs rather than straight stairs, check out the Spiral Stairs Tutorial here.
Accessing Straight Stair Tool
You can access the Straight Stairs Tool from the Home and Extended Modeling tabs.
Accessing Straight Stair Tool from Home tab
Home tab > Extended Modeling panel > Straight Stair
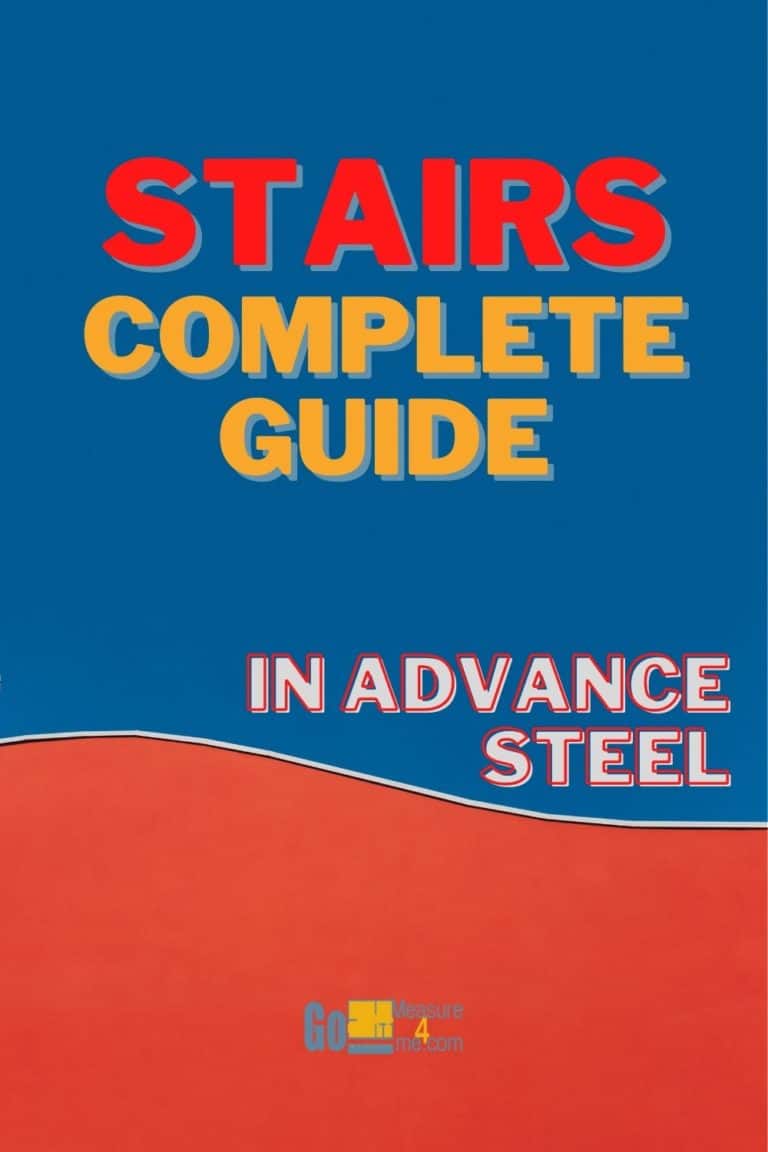

Accessing Straight Stair Tool from Home tab
Home tab > Extended Modeling panel > Straight Stair
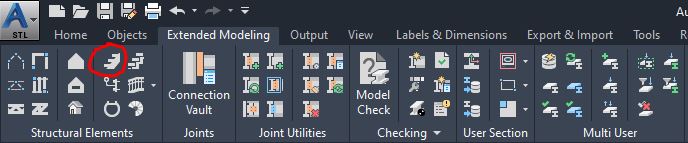
Straight Stair Tool
When using this tool, you can modify all components of the stairs – you can change the stringers, steps, treads, and create landings at the top and bottom. Very important to note – when inserting straight stairs, Advance Steel will insert the stairs in the current UCS (User Coordinate System) plane. There are three ways of creating straight stairs:
- based on start and end points
- based on length and angle
- based on height and angle
When you engage the Straight Stairs Tool, you will be prompted to enter:
Start and end point=0 (default), Length and angle=1, Height and angle=2
Now, you need to decide which option you want to use to create your stairs. By default, the Start and End Point is selected, so when you press ENTER for the first prompt, you have specify the start and end point of the stairs. When you are done specifying these two points, then the following prompt will be displayed:
Align stairs: Left=0, Middle=1, Right=2
At this point, you need to specify the alignment of your stairs in reference to the points you just specified. By default, the stairs will align in the middle. When you press ENTER for this prompt, the stairs will be created with the default options applied, and the dialog box will be displayed:
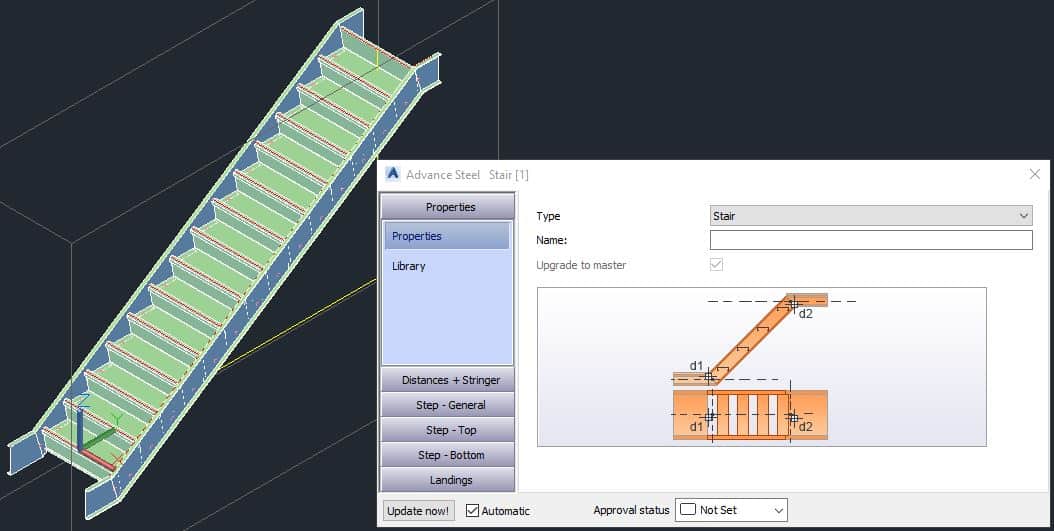
Let’s discuss available options in this dialog box.
Distances + Stringer
Distances + Stringer Tab
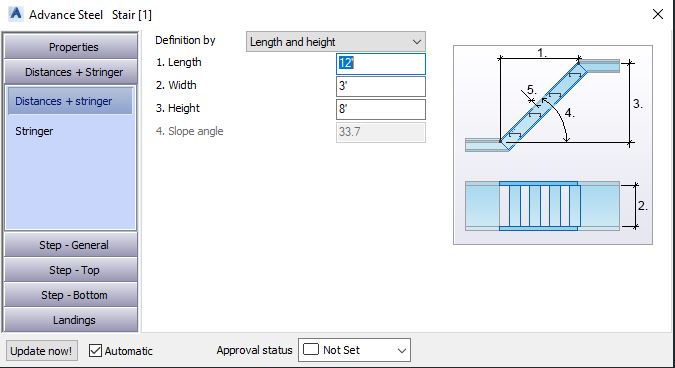
This is to specify how the stairs will be created; by default, Length and Height are selected. The values of the length and height are calculated based on the two points chosen when you created the stairs. Those values can be overwritten using dialog boxes Length (1), Width (2), and Height (3). Also, it is possible to choose two other options: Length and Angle and Height and Angle and specify their values to create the stairs.
Side note: please be advised that some tread types (Step-General > Tread Type) have a predefined width, so when you select those types, the Width box will not be accessible.
Stringer Tab
You will specify here all the stringer options.
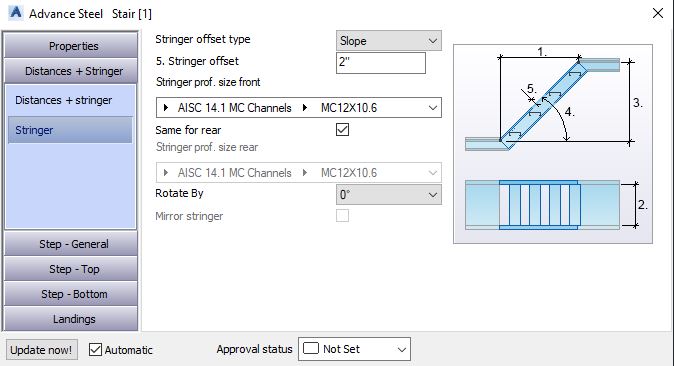
Stringer Offset Type
Specify the offset from the treads. By default, Slope is selected. The other options available are Vertical and Horizontal options.
Stringer Offset
This is where you can specify the Stringer Offset (5) value.
Stringer Profile Size Front
Specify the Type and Size of the Front Stringer here.
Same For Rear
When you check the box, the same profile you specify for the Front Stringer will be used for the Rear Stringer. If you wish to specify a different profile for each stringer, you need to uncheck this box.
Rotated By
Rotate the stringer by predefined angle values that are available in this list.
Mirror Stringer
Check this box to mirror the stringer.
Step - General Category
Step Size Tab
Specify the step size parameters. The default relationship is defined by the formula: 2R+G (R=raiser, G=going). If you wish to create your stairs based on different values, you can enter them here.
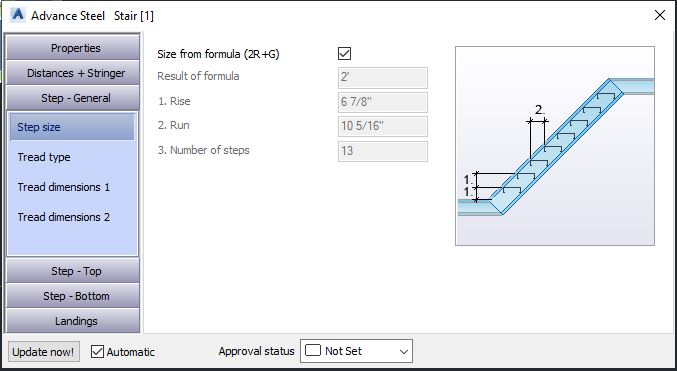
Tread Type Tab
Tread Type
Select the tread type from available options (1 to 24 and 3 obsolete).

Tread Size
Options will change based on the selected tread type.
Connection Tread To Stringer
This list is to specify if you want the tread to be bolted to the stringer or welded. This list might be not accessible for some types of treads.
Offset By Stair Width
Specify the offset value between the stringer and the treads. The width of the treads will be shortened on each side by this value.
Weld Thickness
Enter the weld thickness if the connection requires welding.
Bolt Diameter
Select the bolt diameter from the list for bolted connections.
Bolt Type
Select the bolt type for bolted connections.
Bolt Grade
Select the bolt grade for bolted connections.
Bolt Assembly
Select the bolt assembly for bolted connections.
Bolt/Welds Location
Specify where the connections are to be made: site or shop.
Save
Override the current tread type, size, and connection values in the Tread Size drop-down list.
Save As
You can save a new tread size to then become available in the Tread Size drop-down list.
Rename
Rename the current Tread Size with a different name.
NOTE: Good practice is to save the preferred tread information with the custom prefix (e.g. your initials). This way you can select your preferred tread details by simply selecting them from the Tread Size drop-down list.
Tread Dimensions 1 Tab
Options to specify the tread dimensions and details are available in this tab.
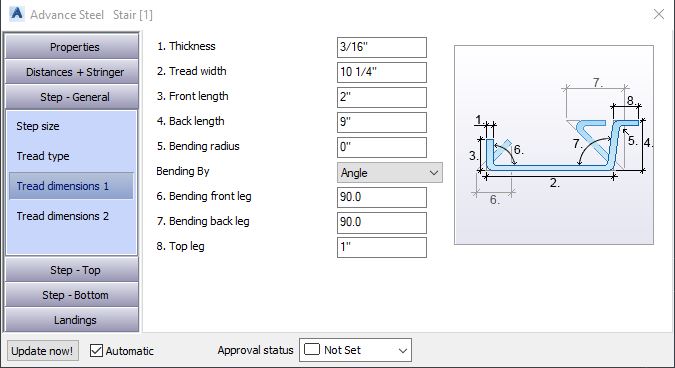
Thickness (1)
Specify the thickness of the tread material.
Tread Width (2)
Specify the widts of the tread.
Front Lenght (3)
Specify the length (height) of the front leg.
Back Lenght (4)
Specify the length (height) of the back leg.
Bending Radius (5)
Bending radius – specify by angle or distance.
Bending Front Leg (6)
Specify the angle of the bend of the front leg. Notice the direction of the bend is shown as a half-tone representation.
Bending Back Leg (7)
Specify the angle of the bend of the back leg. Notice the direction of the bend is shown as a half-tone representation.
Top Leg (8)
Specify the height of the back leg.
Tread Dimensions 2 Tab
Specify the tread side, bolt location, and corner size. The available values depend on the type of tread chosen in the Step-General > Tread Type tab.
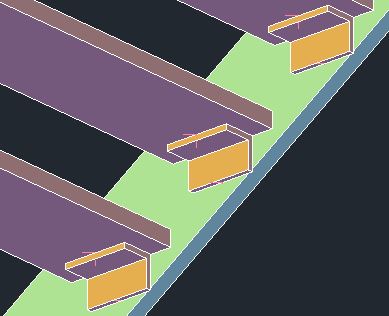
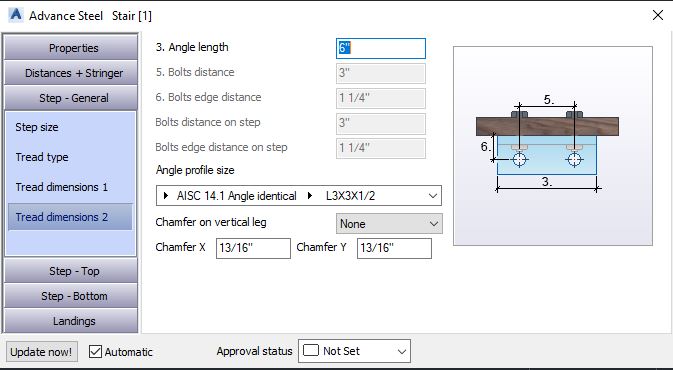
Angle Lenght (3)
Specify the total length of the angle.
Bolt Distance (5)
Specify the distance between the bolts.
Bolt Edge Distance (6)
Specify the distance between the bolts and tread.
Angle Profile Size
Choose the profile of the member.
Step-Top/Step-Bottom
The options available here are to specify the details of the top and bottom treads. By default, the Same as Other Step check boxes are selected, and other options are greyed out. If you wish to create different steps, you need to clear the check boxes and tweak the available options.
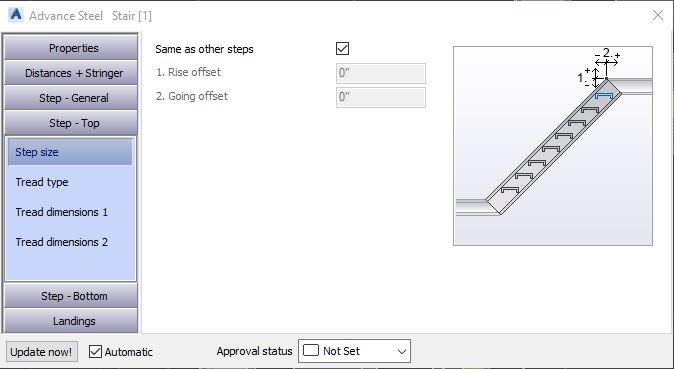
Landings
Top Landing Profile
Determine here if you wish to create a Top Landing and select the Top Landing profile.
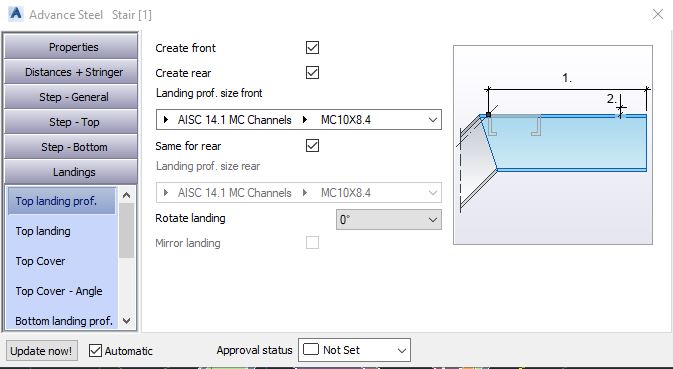
Create Front / Rear
Create Front/Rear by checking these boxes.
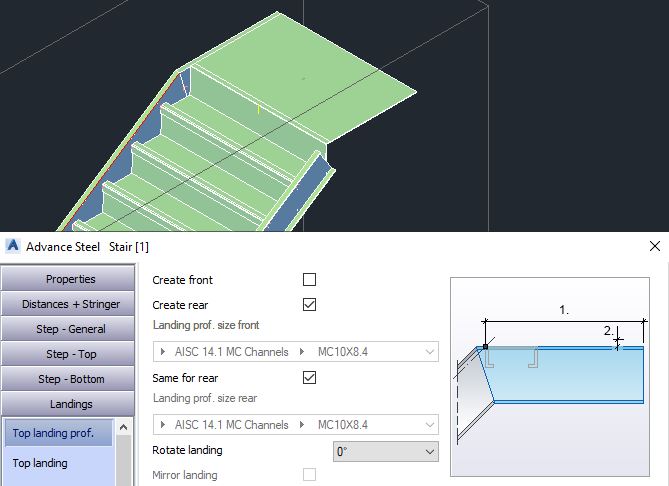
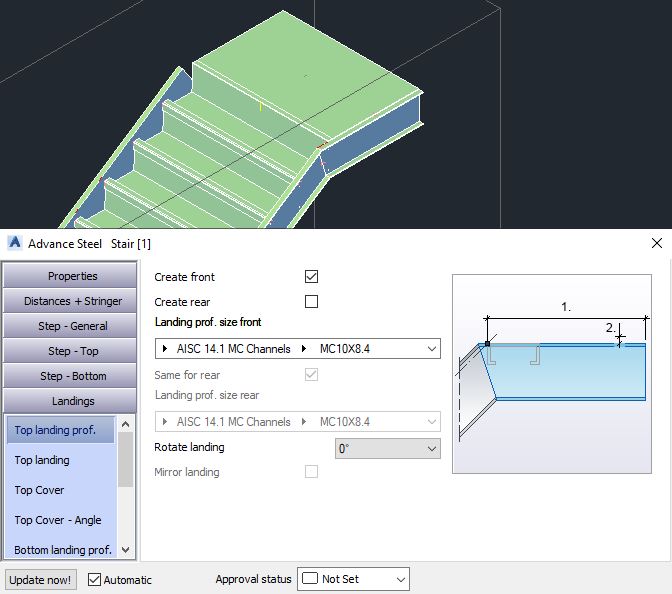
Landing Size Front Rear
Select the desired steel profile for the front and rear.
Rotate Landing
Rotate Landing by predifined values 0, 90, 180, 270 degrees.
Mirror Landing
You have an option to mirror the landing when you check this box.
Top Landing
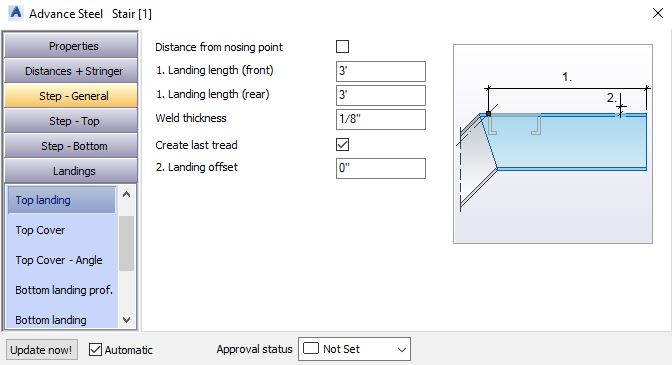
Distance From Nosing Point
Select this box if you rather wish to measure the length of the landings from the nosing point.
Landing Length (front)/Landing Length (rear)
Specify the measurements of the front and rear landings at the top.
Weld Thickness
Specify the weld thickness between the top landings and the stringers.
Create Last Tread
Specify here if you wish or not to create the last tread.
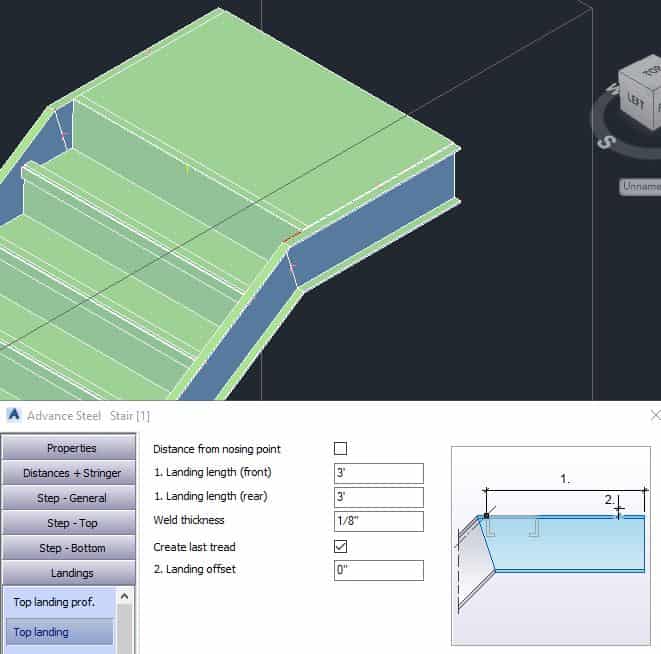
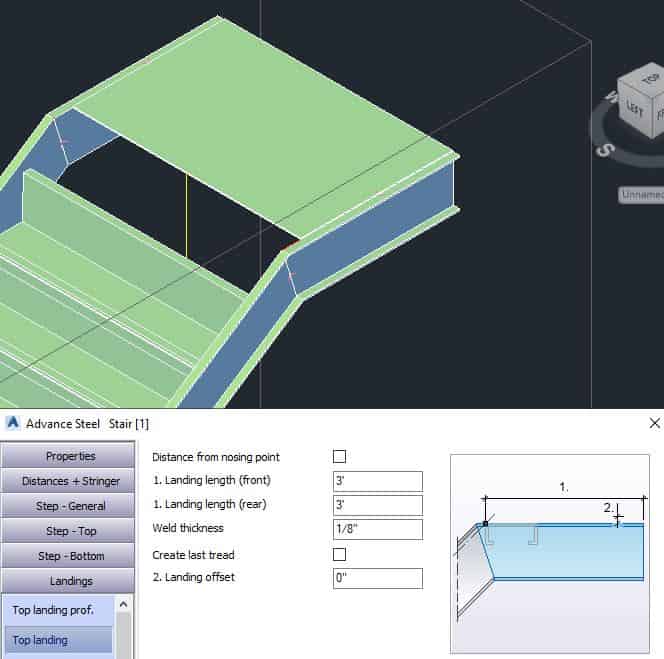
Landing Offset (2)
Define landing offset from the stringer.
Top Cover
Cover Made From
Determine here if you wish to create a top cover and specify what kind of top cover you prefer. Options available: Plate, Grate, Angle No Plate. Angle No Plate will result in angle sections being welded to the top landings, but the plate will not be inserted.
Cover Thickness
Define the thickness of your cover.
Grating Class / Grating Size
When you are using a grating as a top cover, you have an option to select the grating class and size from the lists.
Cover On Top Of Stringer
By selecting this box, you will ensure that the cover is placed on top of the stringer. See pictures below:
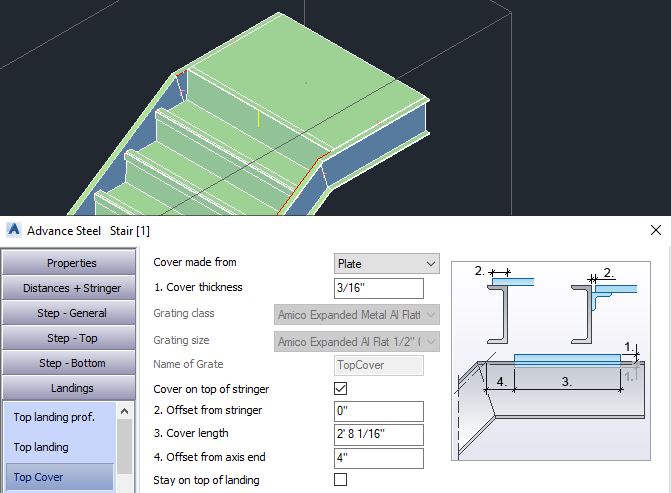
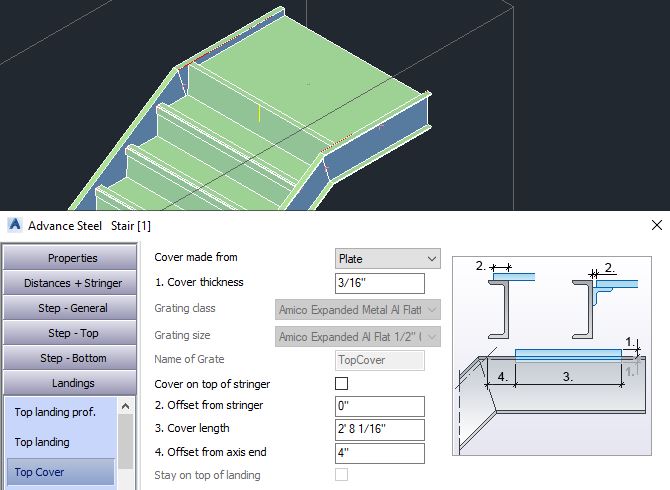
Cover Length
Define the length of the cover.
Offset From Axis End
Specify the offset of the cover from the end of the top landing axis.
Stay On Top Of Landing
This is used when you have selected the Cover on Top of Stringer check box and ensured that the top of the stringer is aligned to the top point you selected when inserting your stairs. The top cover will be above the top point.
Top Cover - Angle
Specify the member profile, weld thickness, and offset from the top (1).
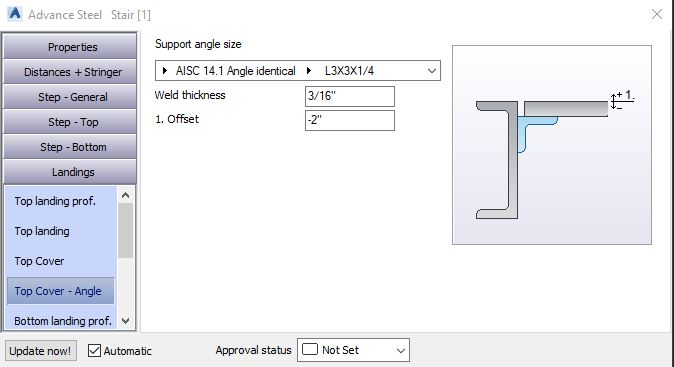
Bottom Landing Profile
The bottom landing profile options are the sister options of the top landing described above. Feel free to use them as the guide.
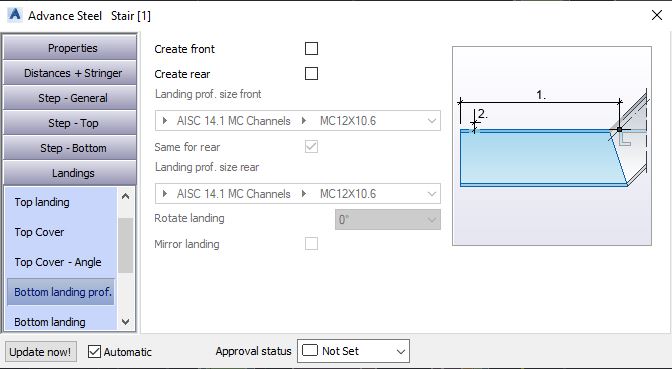
Inserting Base Plates at the Bottom of the Stair
If you wish to place the Base Plates at the bottom of your stairs, the first thing you need to do is place the UCS at the point where you wish to place the plates.
- Type the UCS and select the point.
- Go to the Home tab > Extended Modeling panel > Connection Vault

- Once the Connection Vault is open, go to Miscellaneous and find the Stairs Anchor Base Plate at the top:
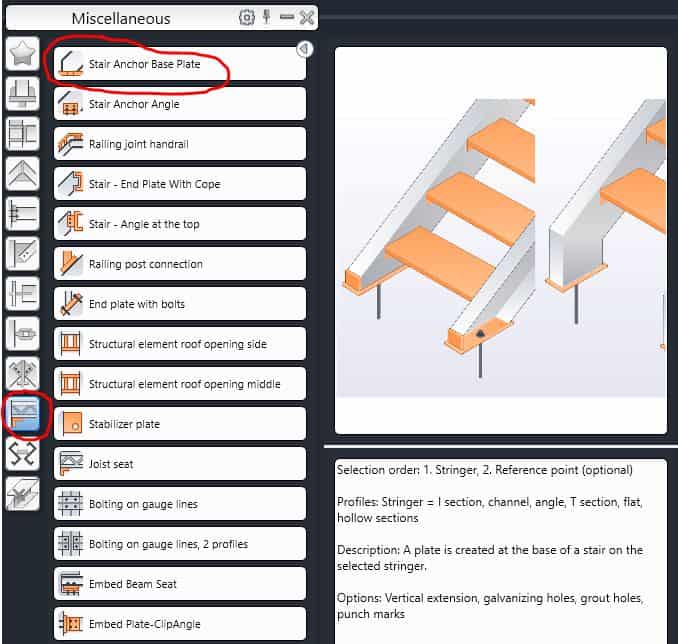
- You will be asked to select the object you want to place at the connection. Select the stringer where you want to place the base plate and press ENTER.
- Specify all the details in the available tabs on the left side of the dialog box:
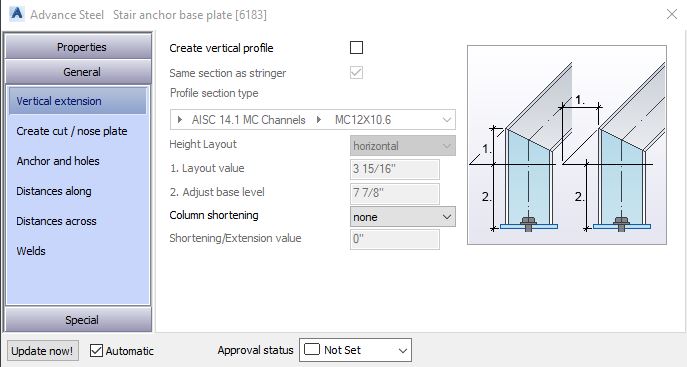
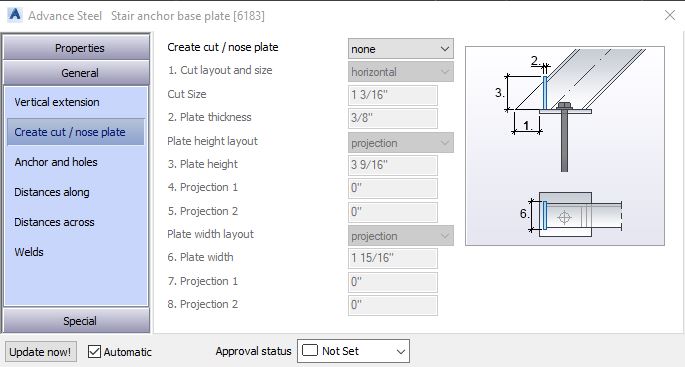
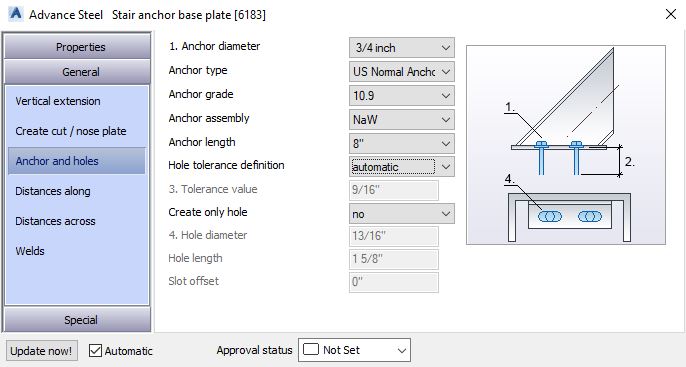
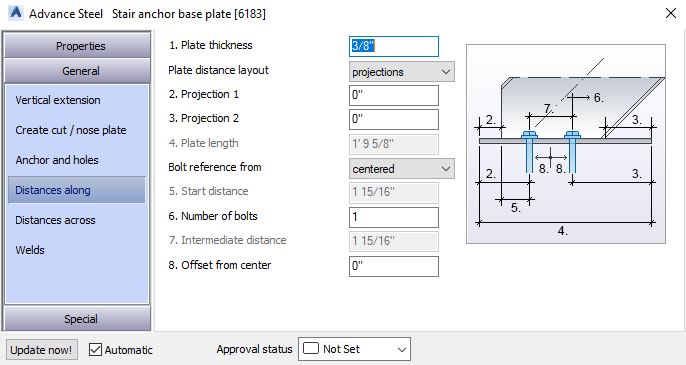
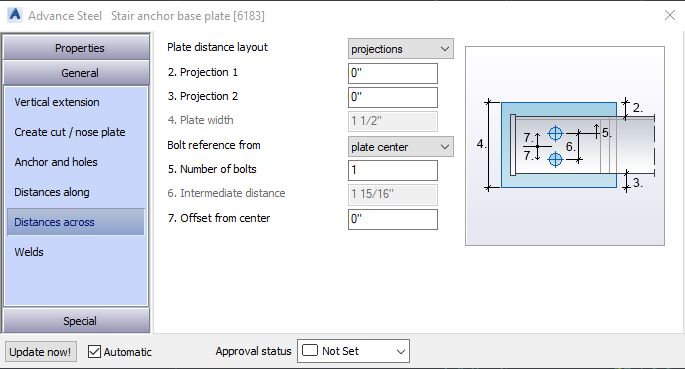
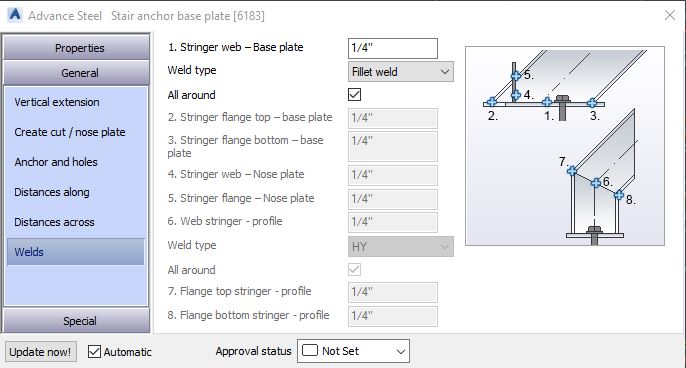
Example with 1′-0″ Cut Size:
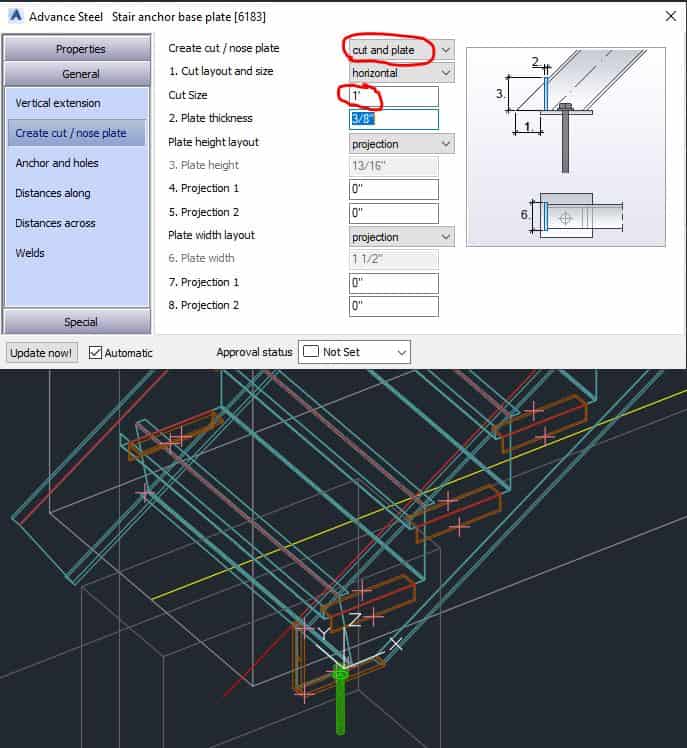
Once you are done defining all the parameters, you can copy this connection to the other side using the Copy with an Adjustment tool. Select your connection box, specify the stringer as a reference object, and specify the other stringer as a target object. However, if the other side gets a different connection, you need to do it from the beginning.

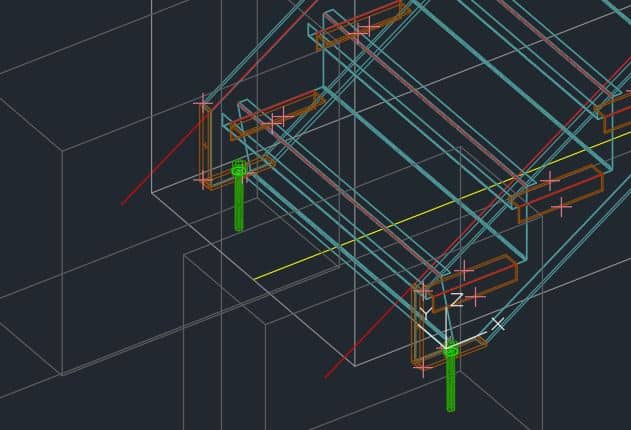
Extending And Cutting Off The Stringers
If you wish to modify the stringers, the easiest way to do this is to use the Shorten at USC tool available in the Advance Steel Tool Palette > Extended Modeling panel > Advance Steel Tool Palette.

When you open Advance Steel Tool Palette look for it at:
Features > Shorten at USC
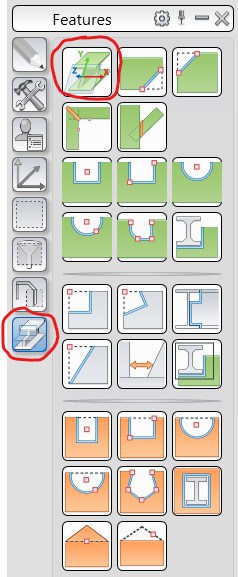
In order to extend the stringer to the plane, first you need to place the UCS at the point where you want to extend the stringer using UCS tool. Simply type in the command UCS and place it where it needs to be placed:
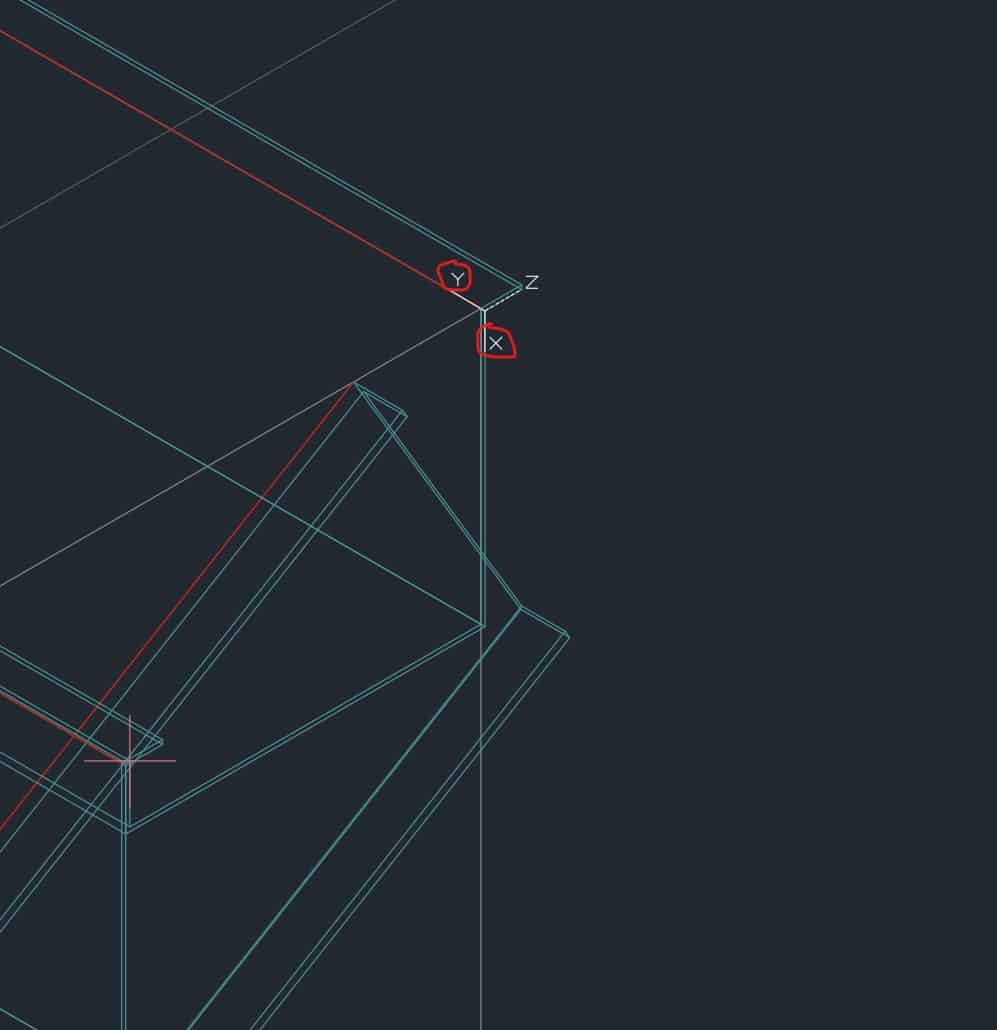
The next step is to start the Shorten at UCS tool. You will be asked to specify the object you need to modify. Select the stringer and press ENTER. Your stringer will be modified to your needs. The tool is extending/trimming the object to the specified X,Y plane.
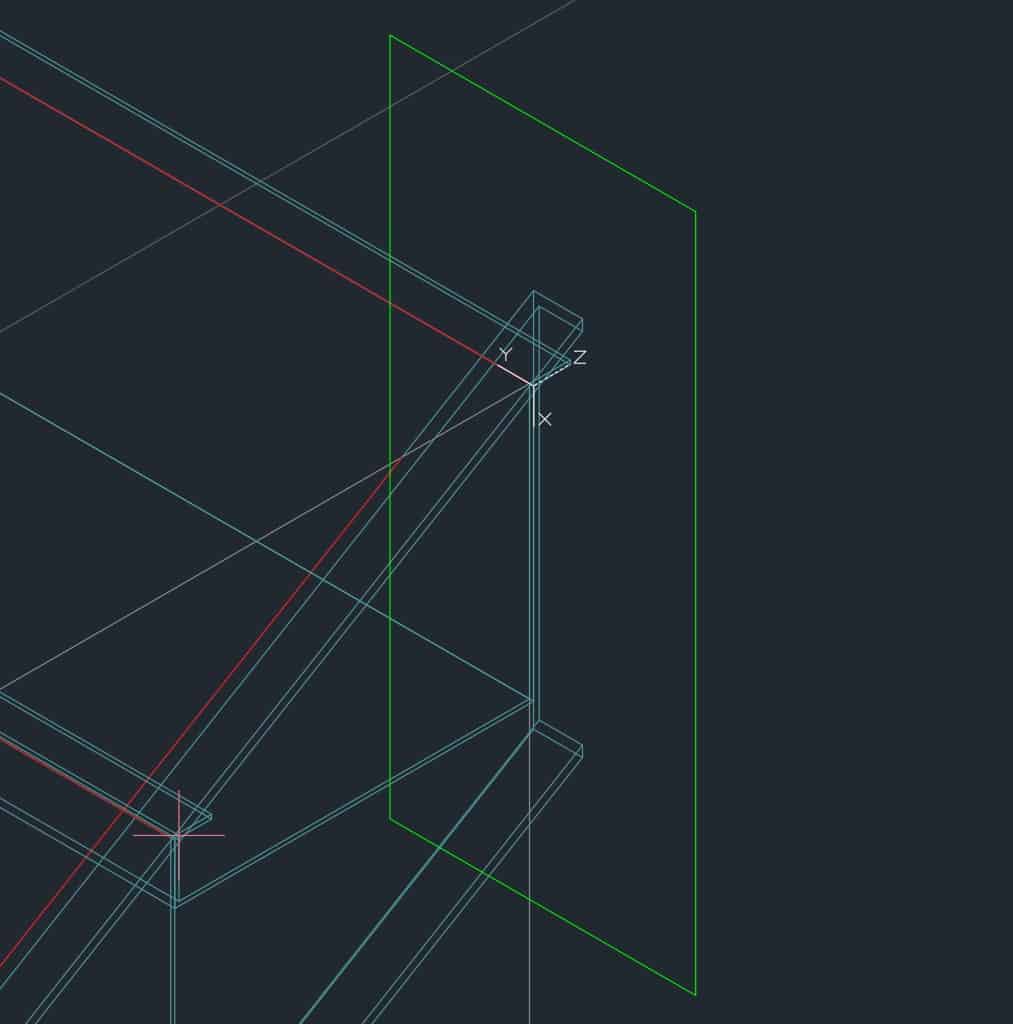
To trim the top part, simply turn the X, Y plane to the vertical position and use the tool again.
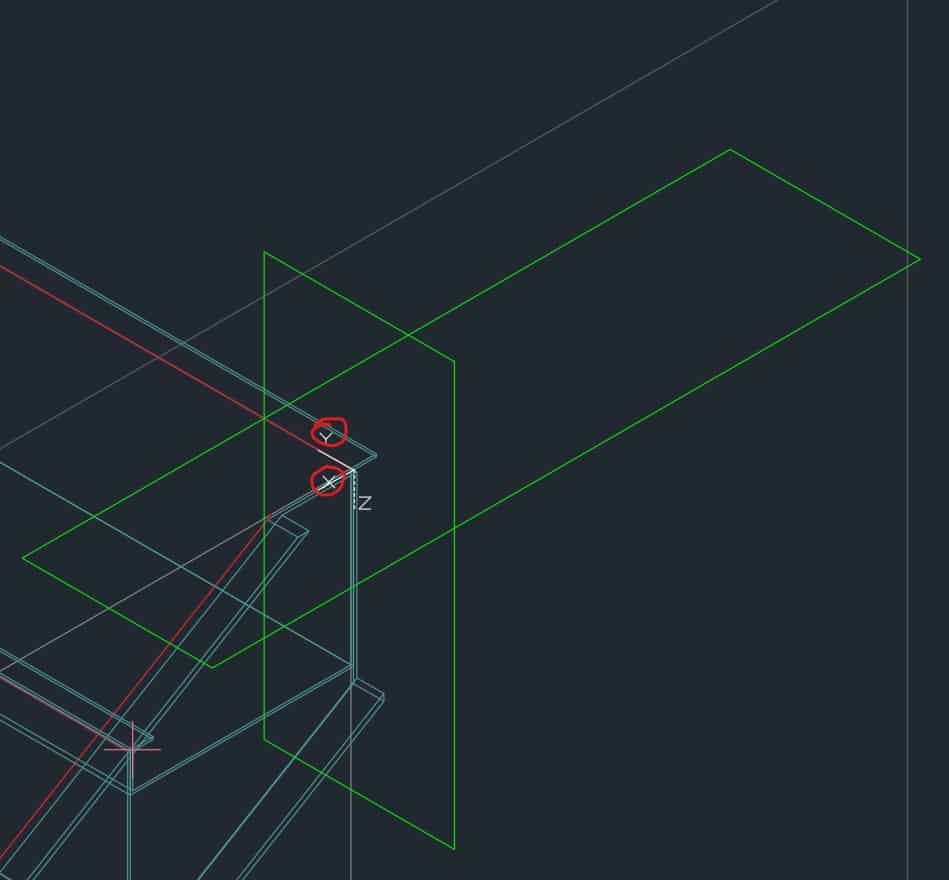
The stringer trimmed in both planes:
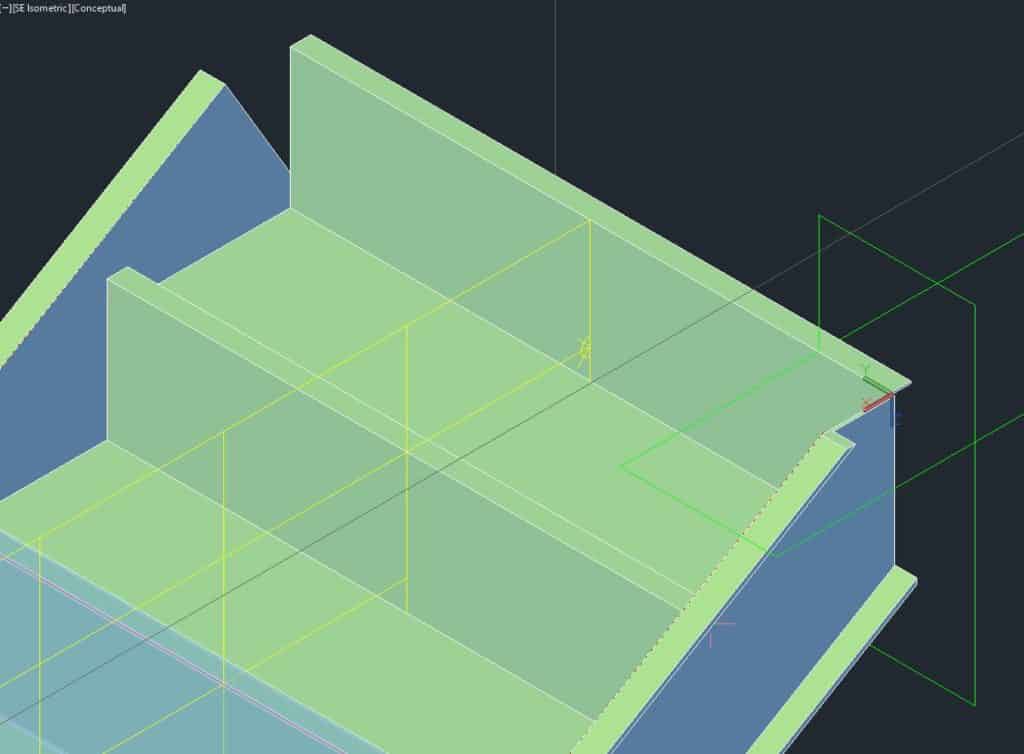
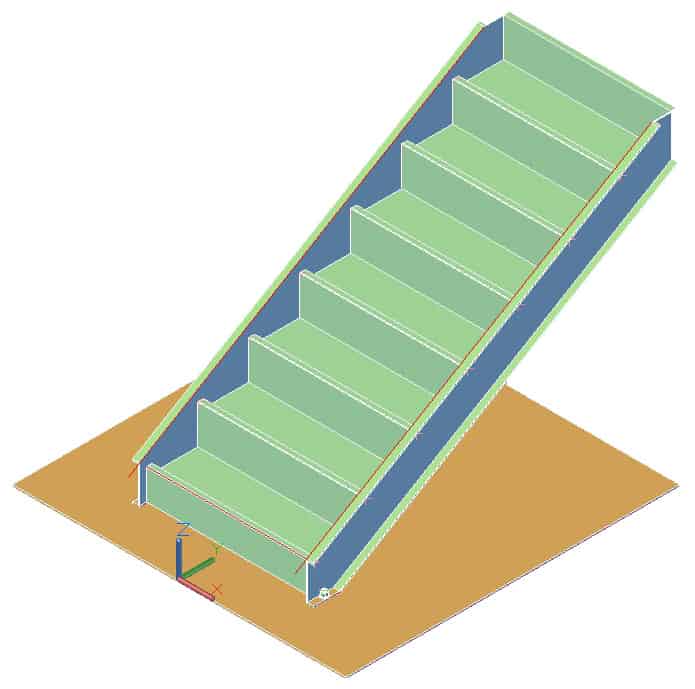
The stairs most likely need a railing. Here is a link to my Hand-Railing Tutorial in Advance Steel
This concludes the Stairs in Advance Steel Tutorial. Good luck using all the methods and tools described above. If you found this article valuable, please subscribe to my blog to be notified whenever I publish a new article.
If you are interested in upgrading your hardware or software, make sure to check out My Toolbox article, where I share information about the tools I use and special discounts you can use as well.
If you are into Advance Steel –